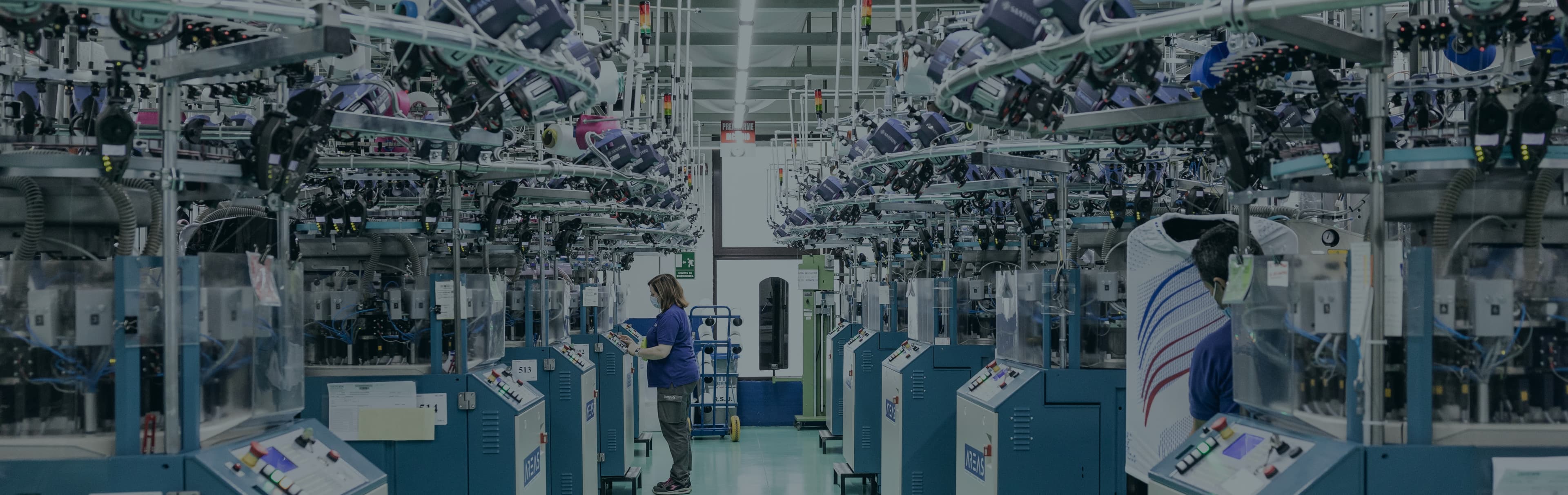
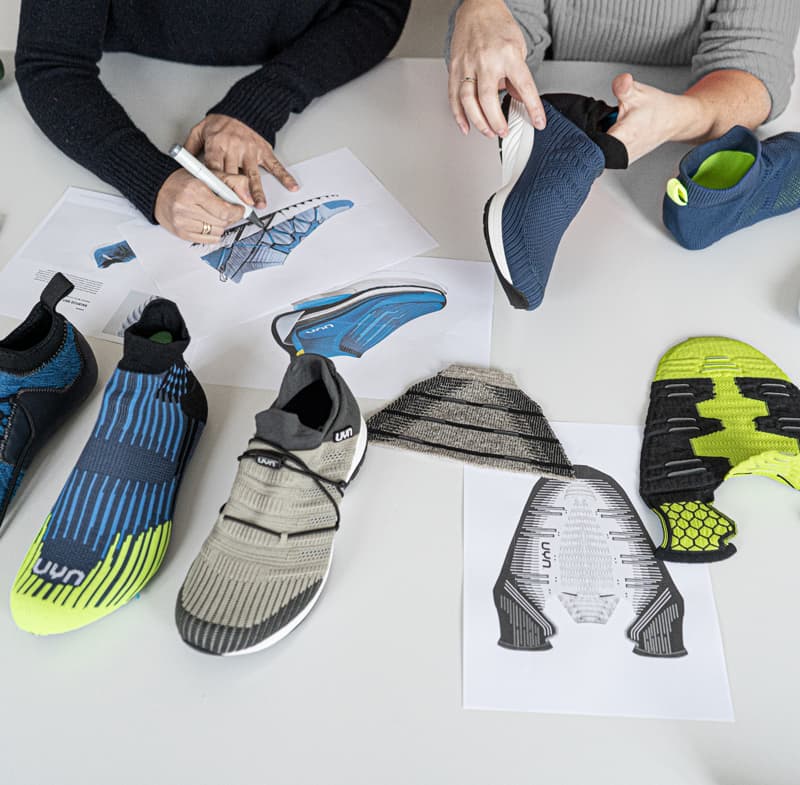
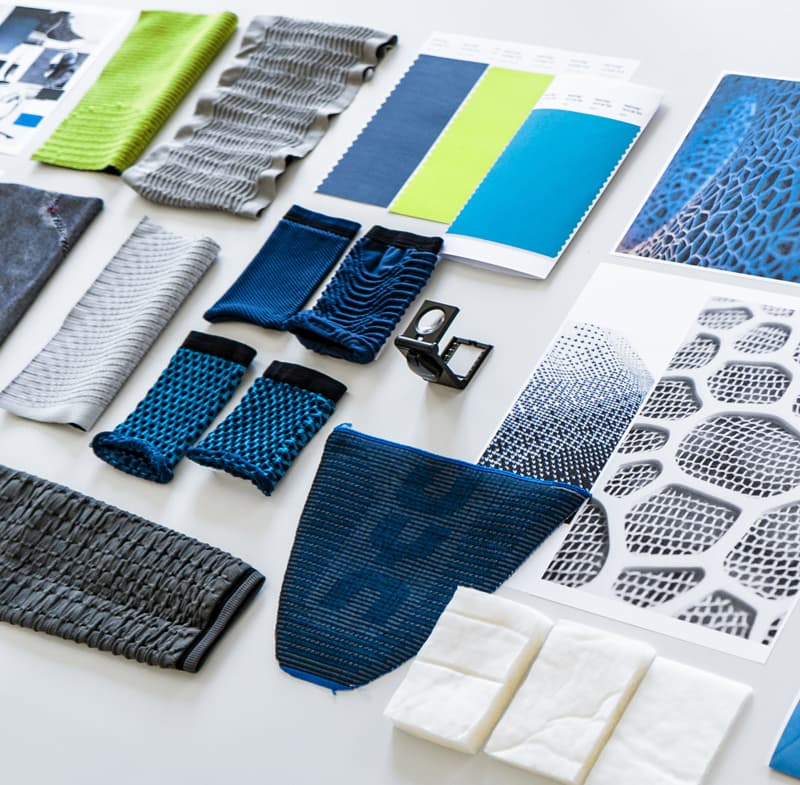
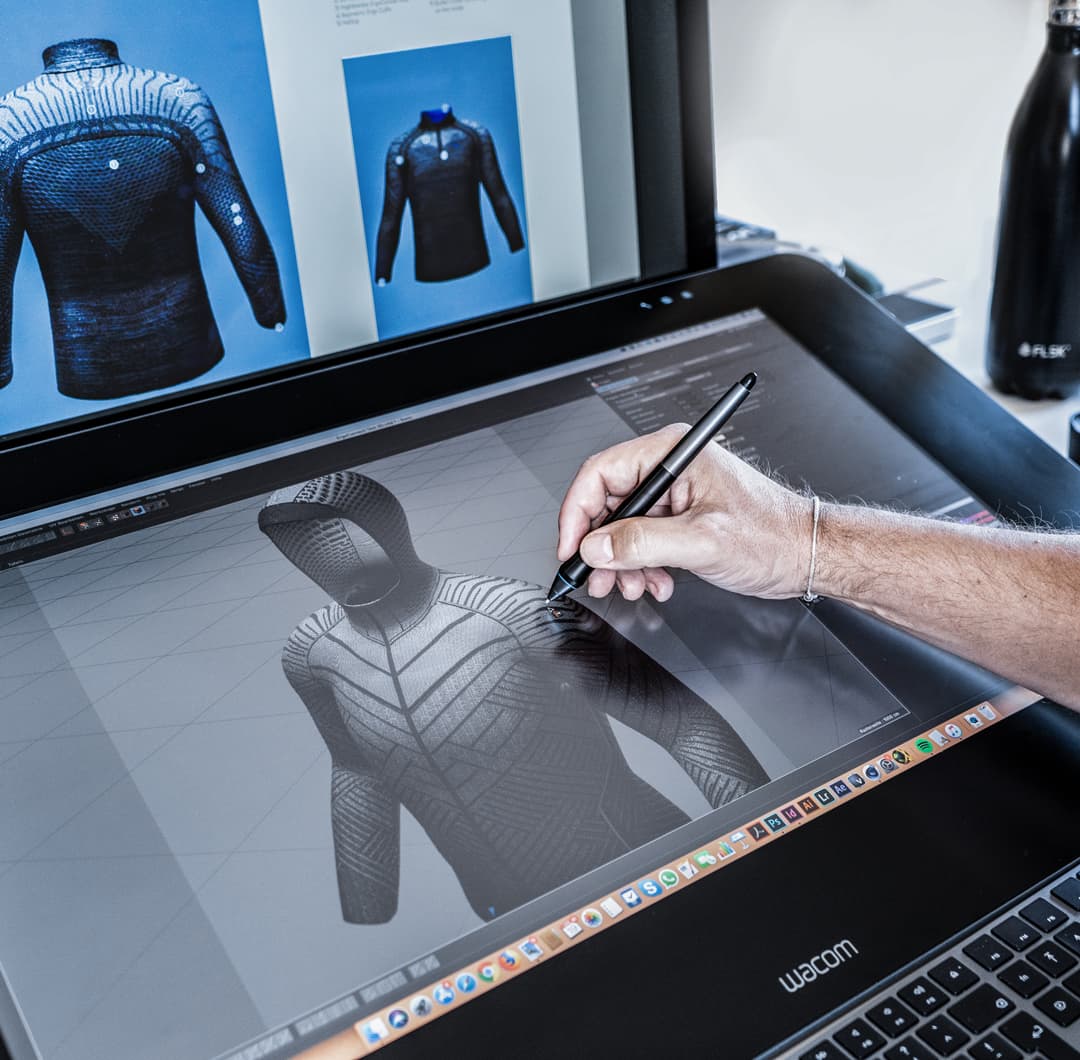
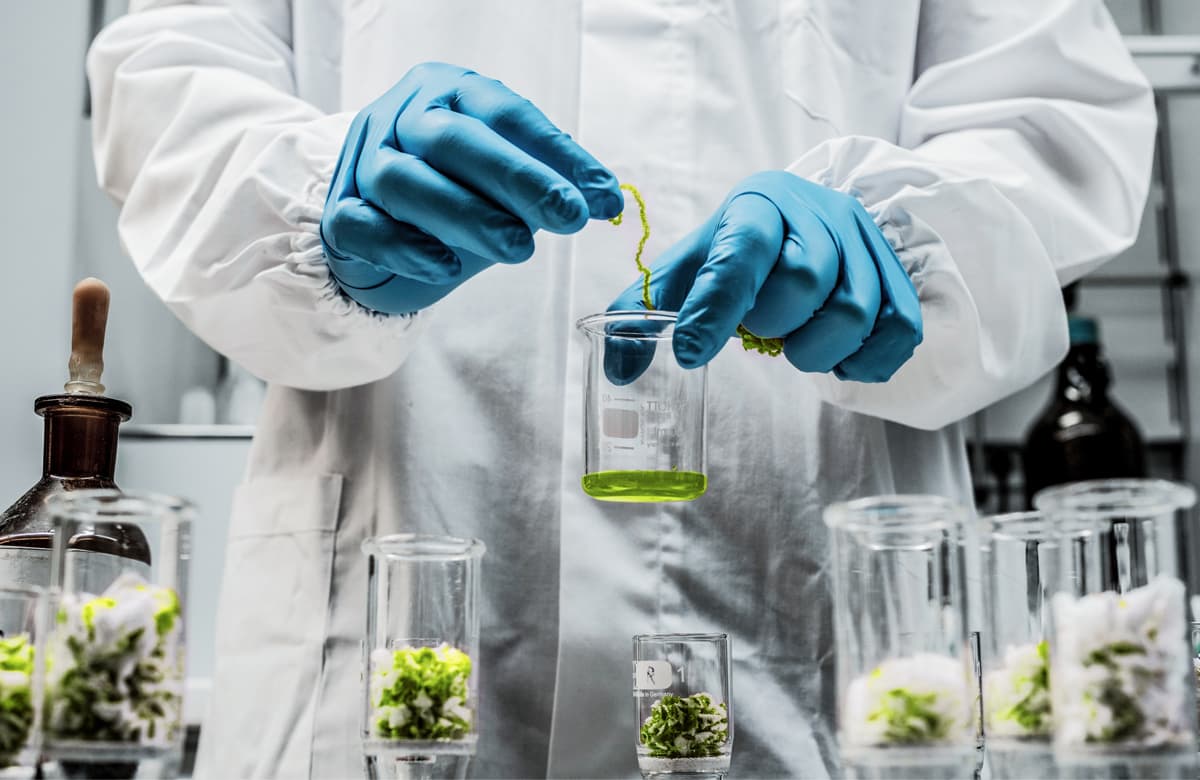
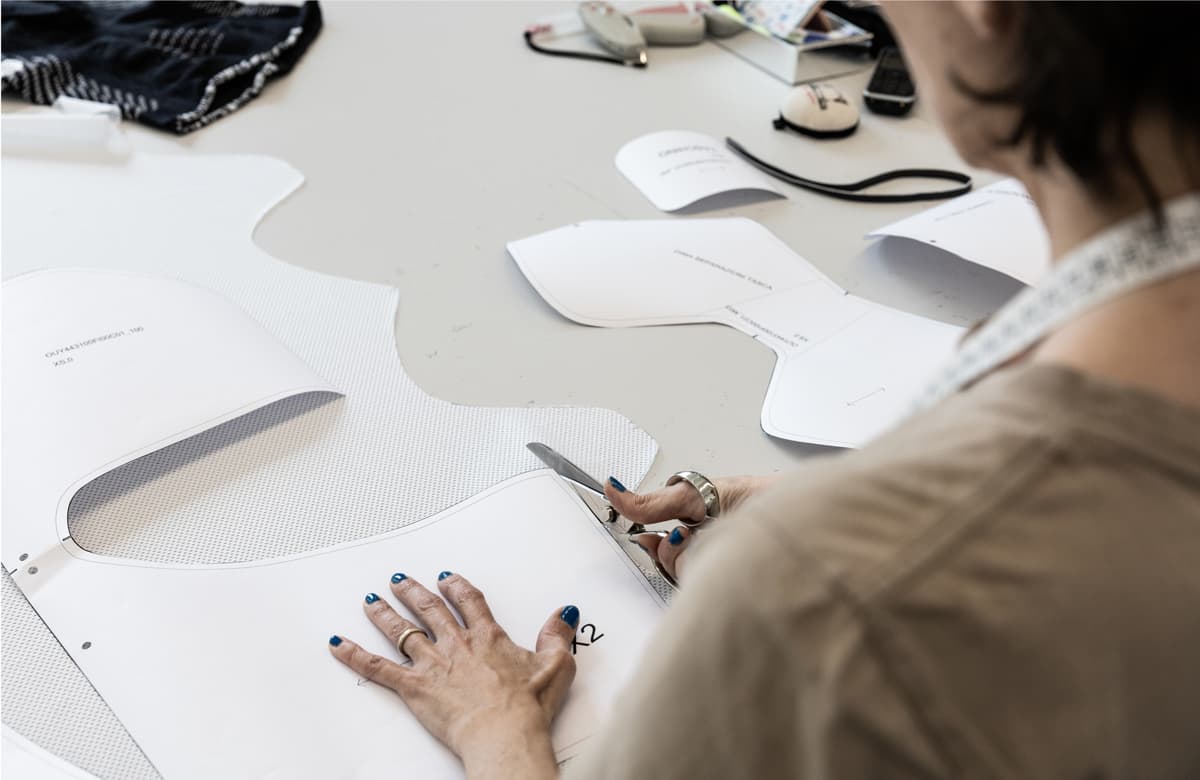
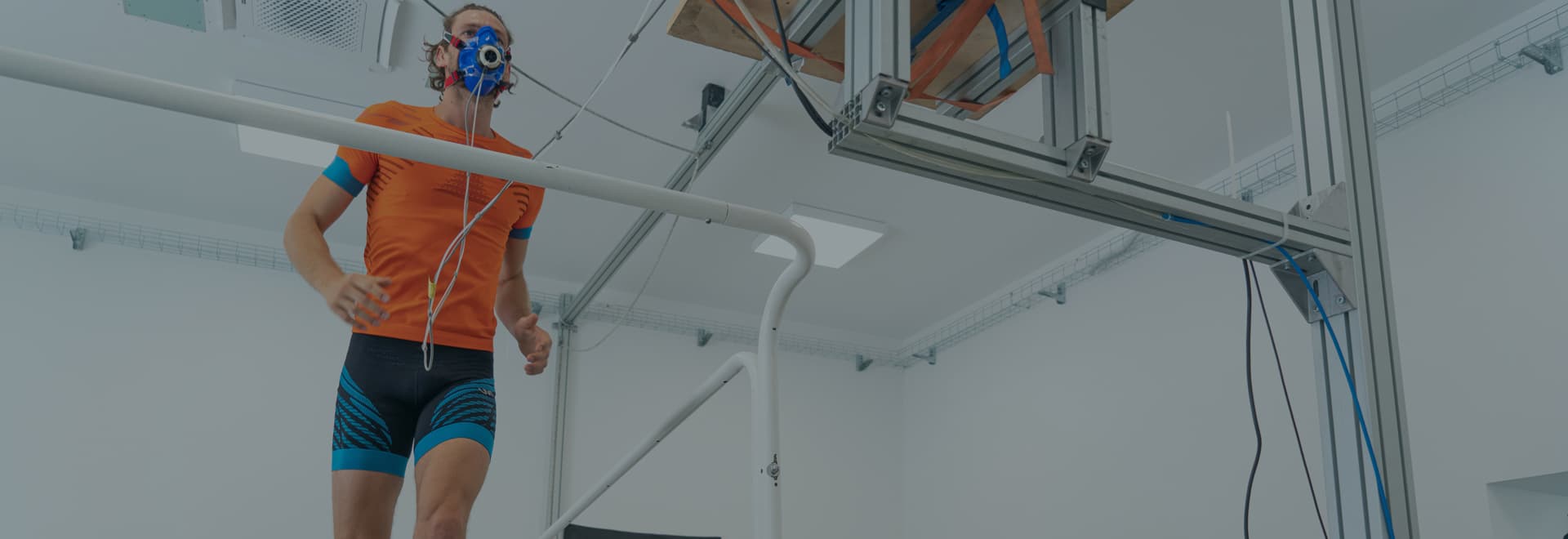
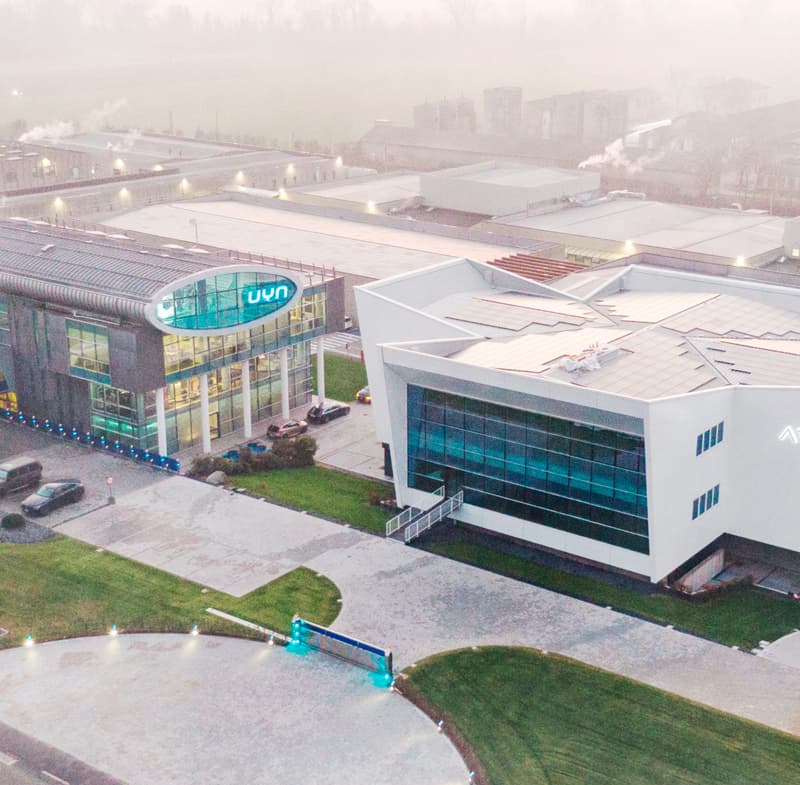
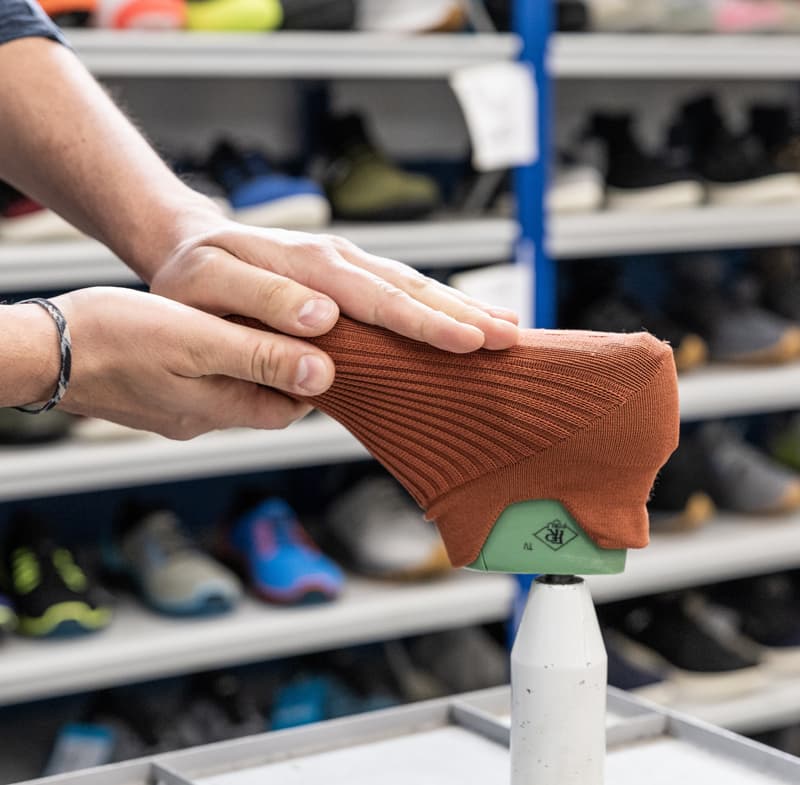
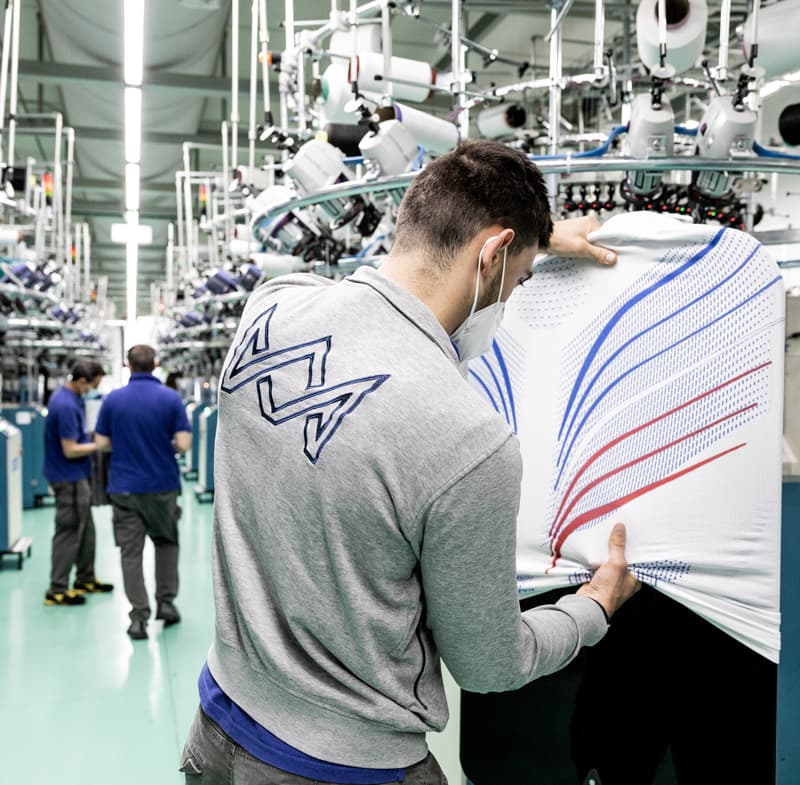
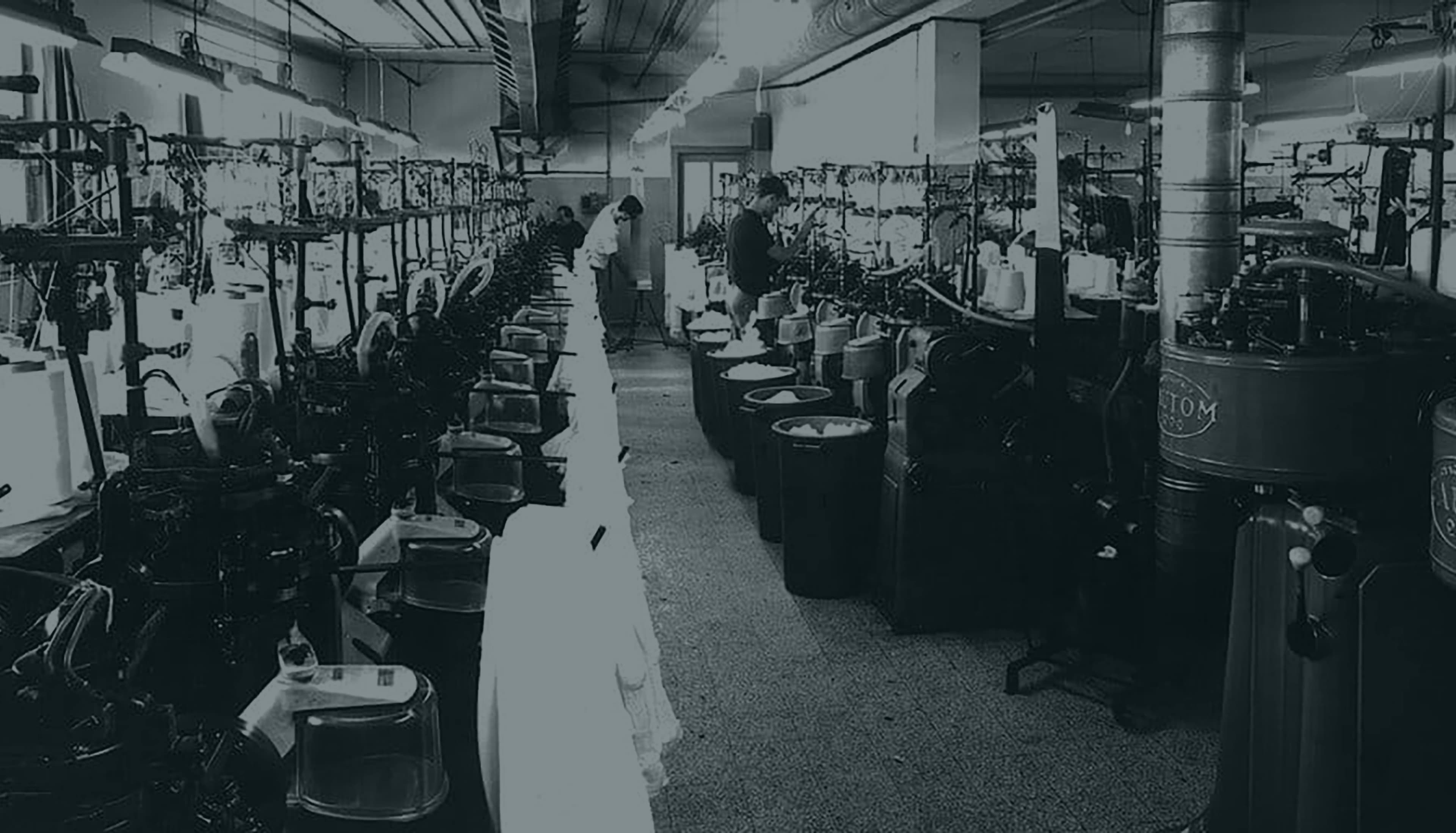
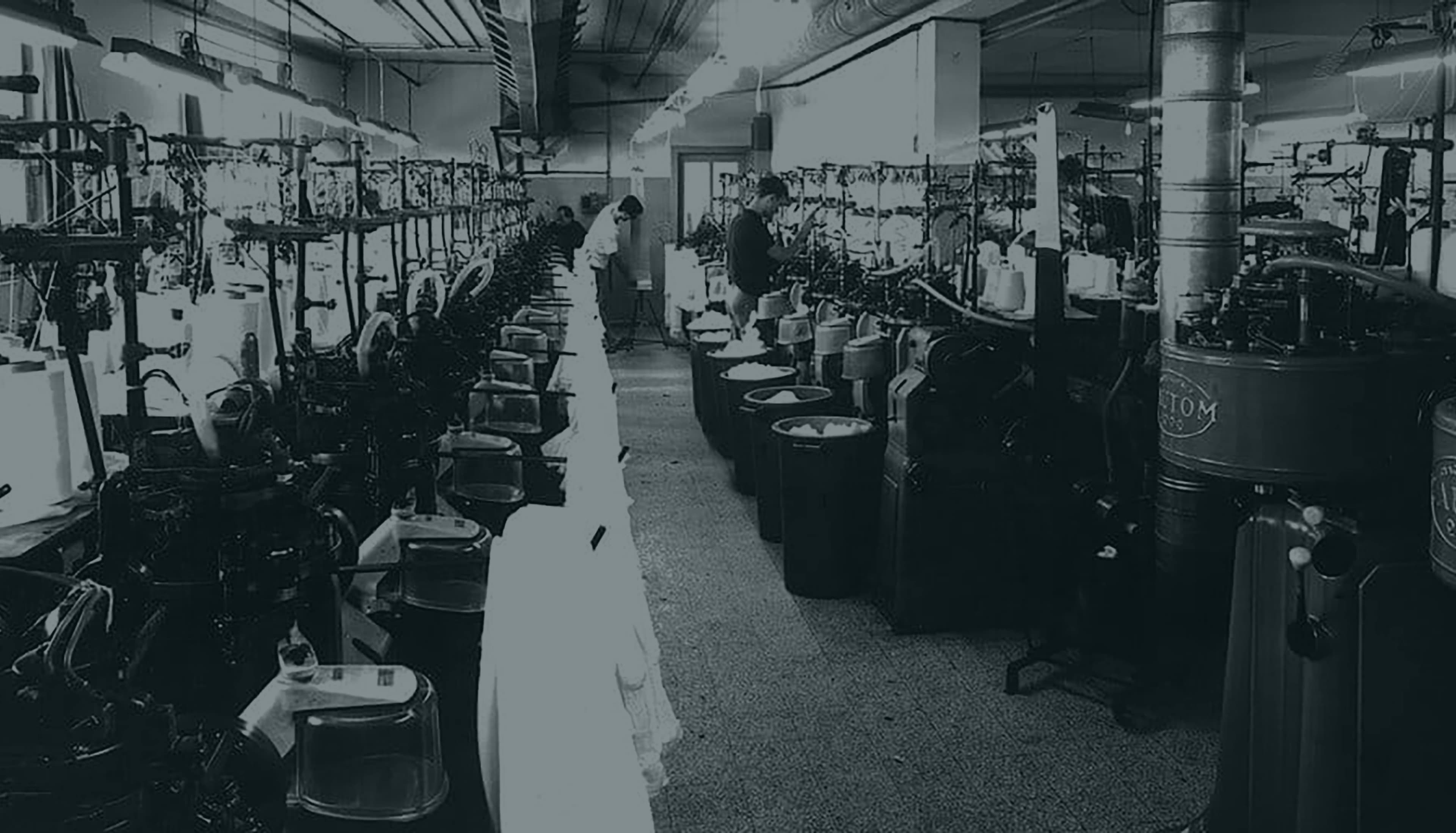
History
MORE THAN 70 YEARS OF EXPERIENCE
The history of great family businesses is the history of values, secrets and motivations passed down from generation to generation, creating a treasure trove of knowledge and passion that is the main asset of any business.
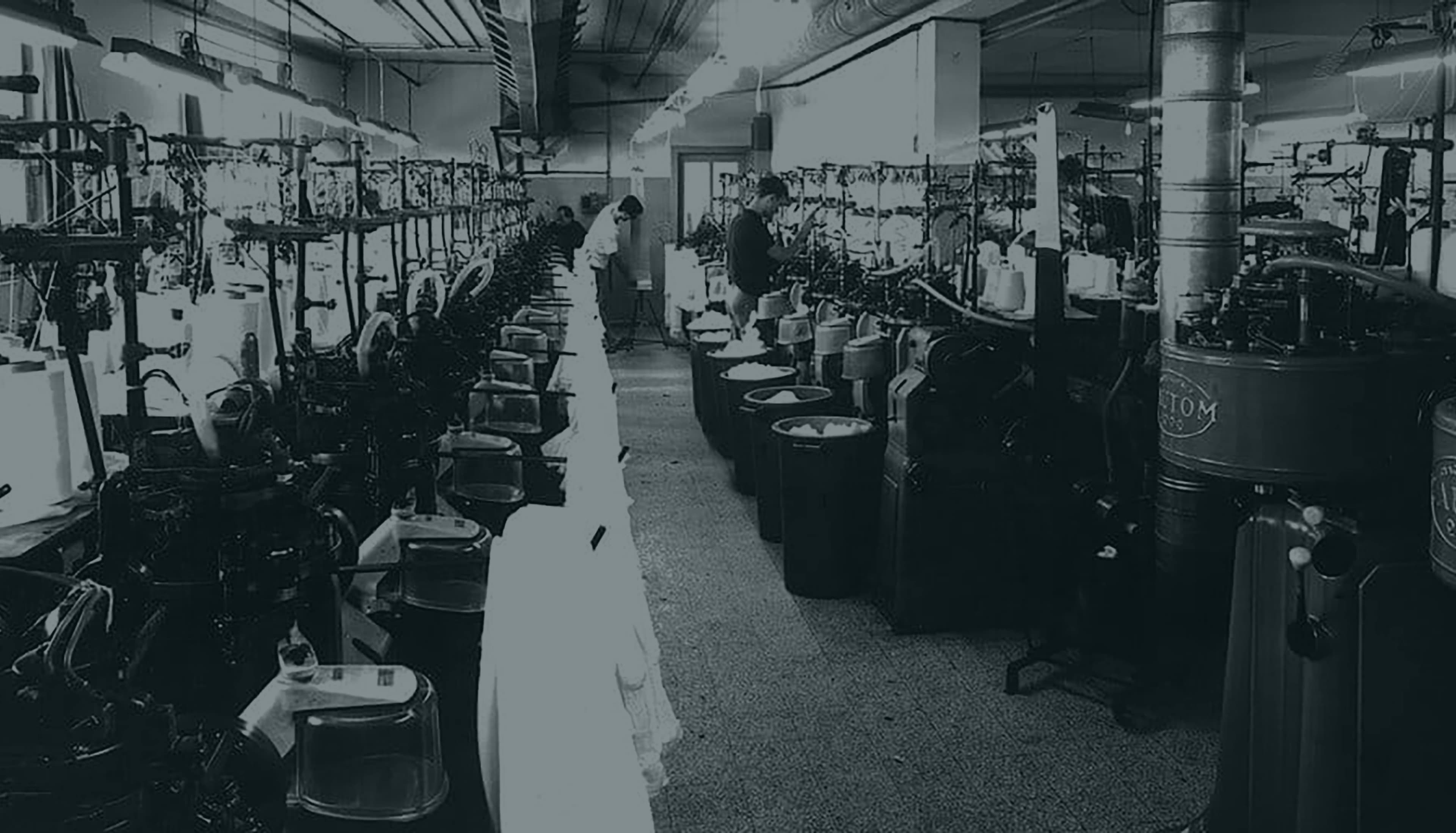
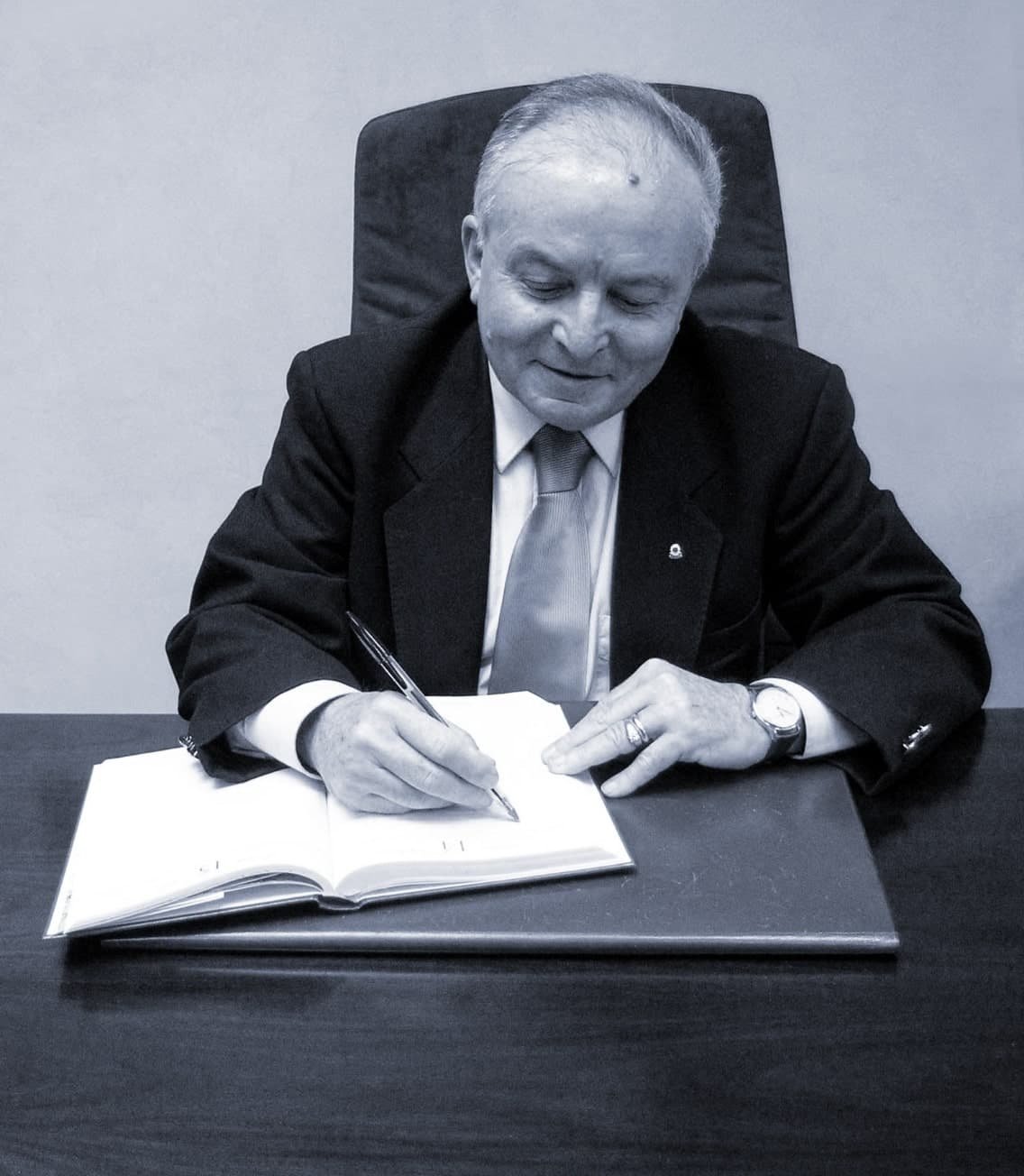
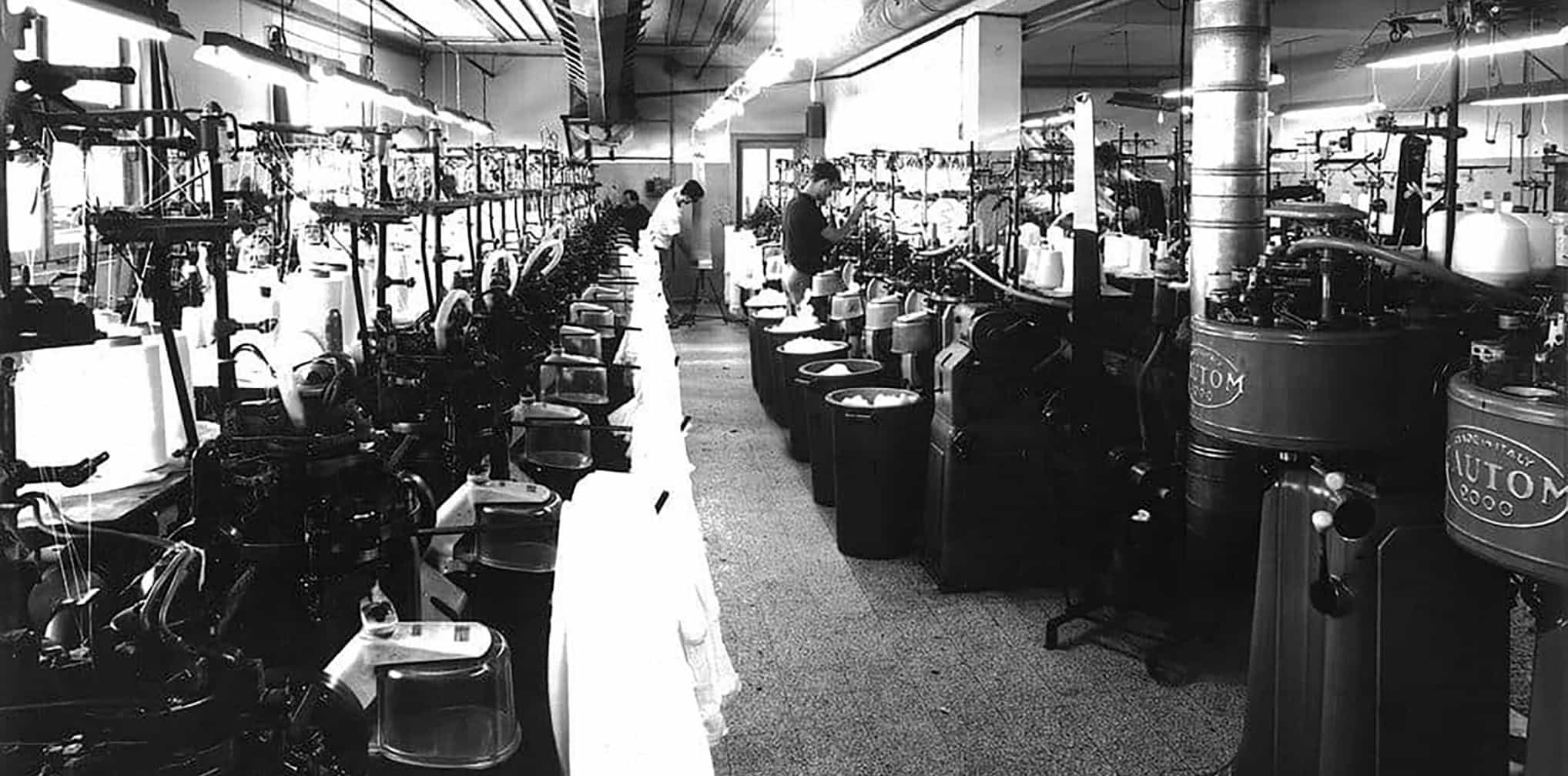
Company formation
Mr Luigi Redini together with his father and brother set up the family’s first company, Selvocalze. This was at the end of the 1950s, when the market for hosiery was growing rapidly. The company took advantage of this great opportunity by starting production with new machinery and, being the first of many who started similar initiatives, it established new quality standards.
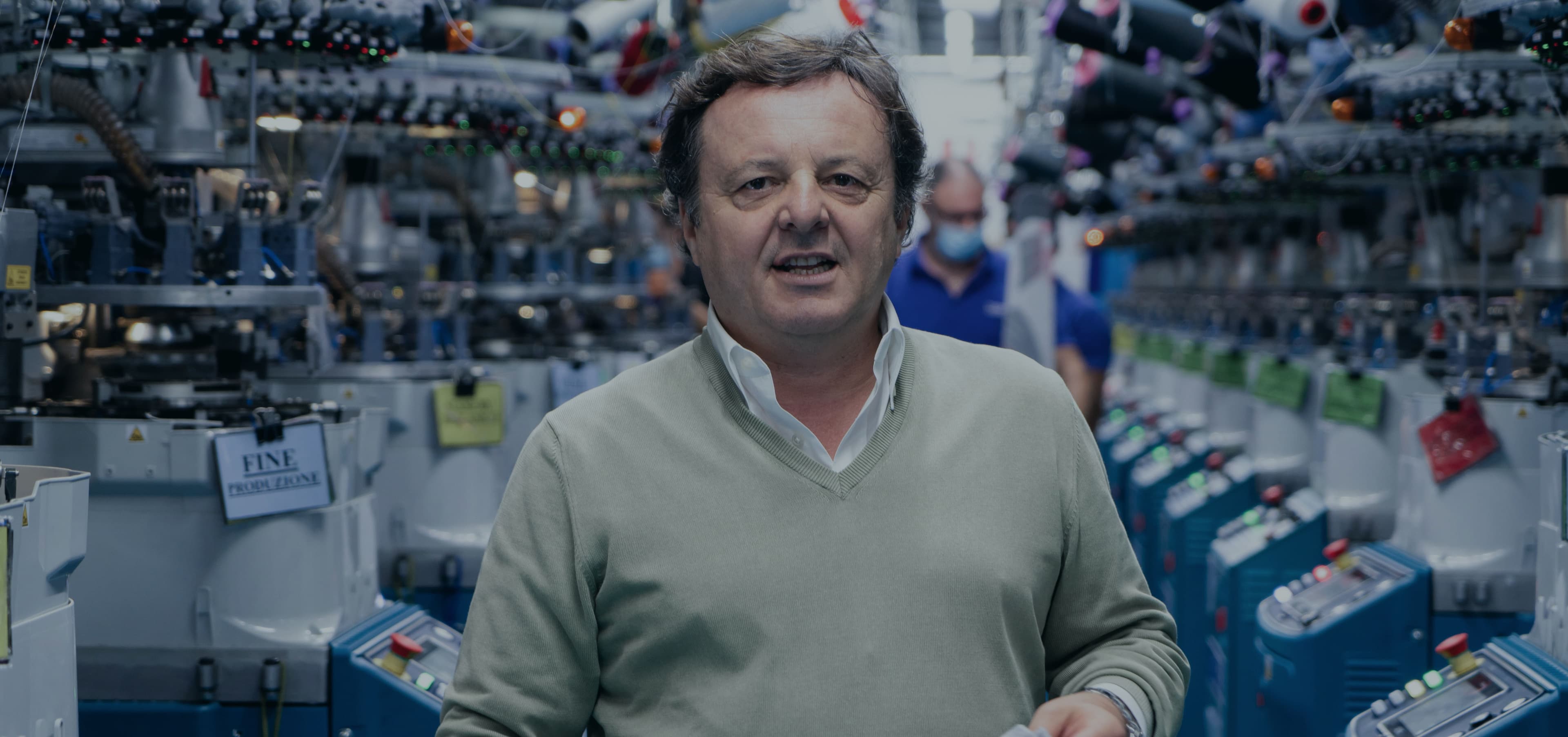
Marco Redini joined the Company
This was at the mid-1980s when sport was playing an increasingly important role in the world of clothing. lt was the start of a period of unprecedented growth, based on research and the discovery of innovative new Materials that would have lead to the expansion of an attentive and evolving market.
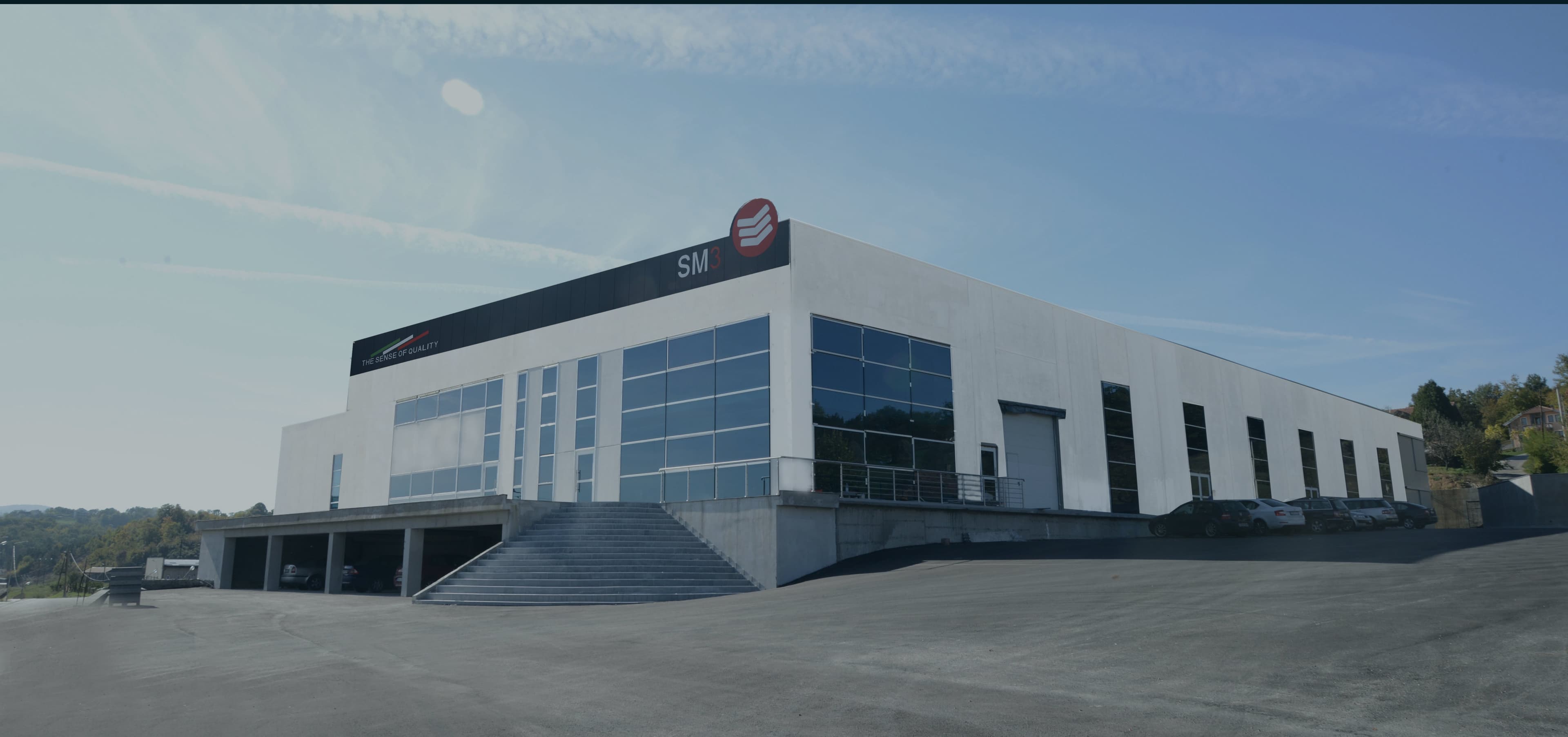
The SM3 was founded
Today, the production site in Bosnia, covering 50,000 m2, has over 550 Trerè employees. It handles cut and sew, seamless, socks and proprietary thread.
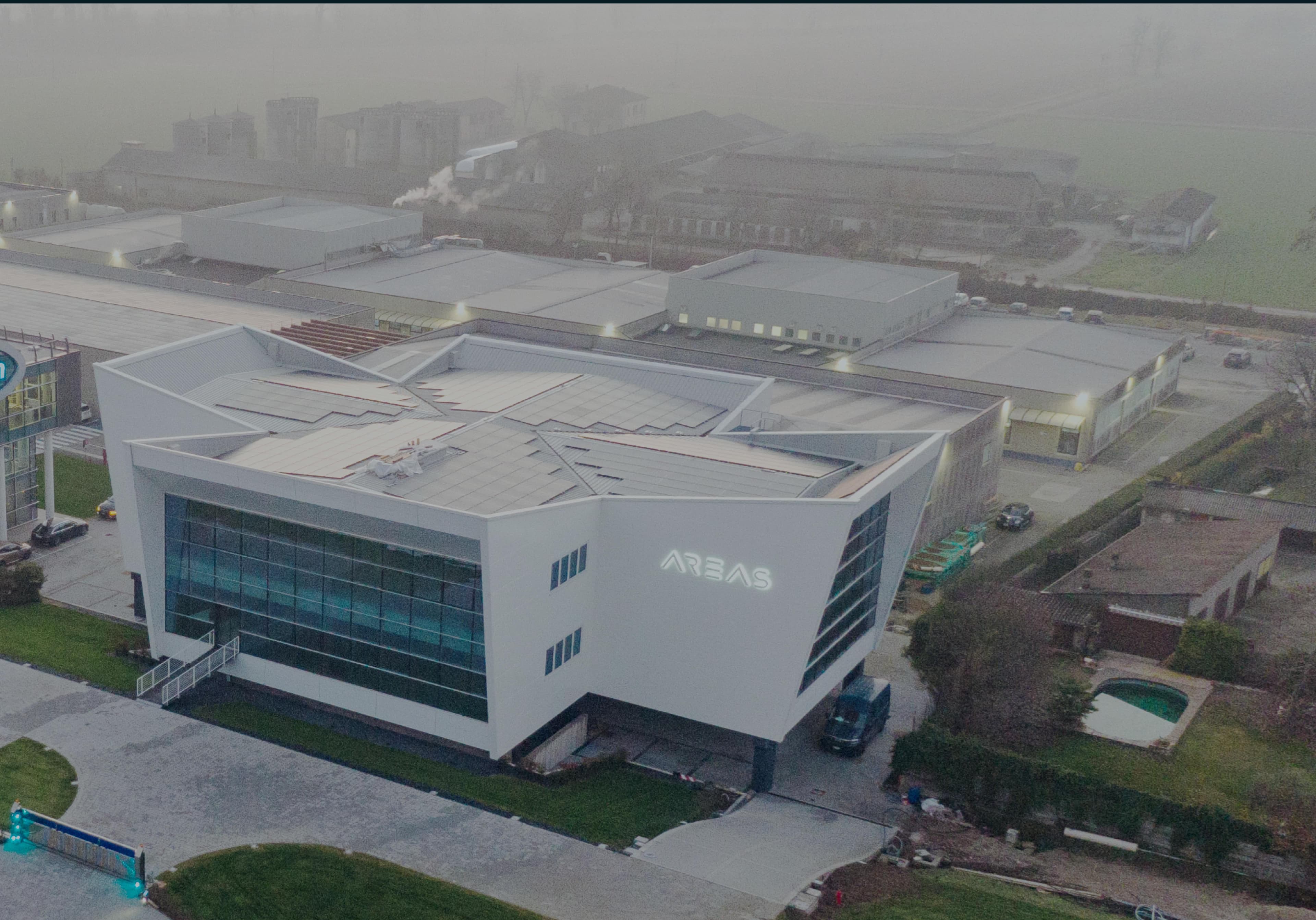
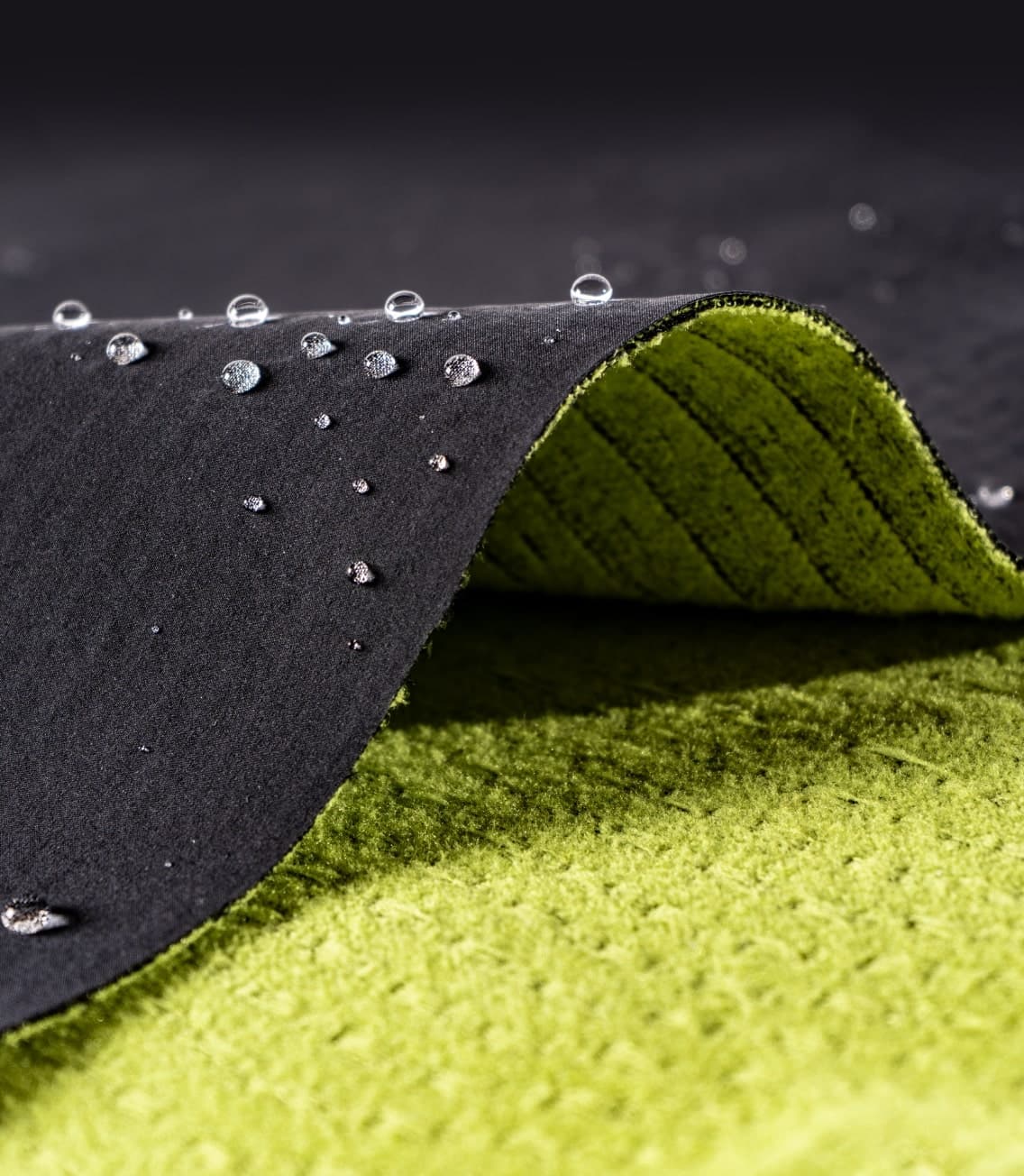
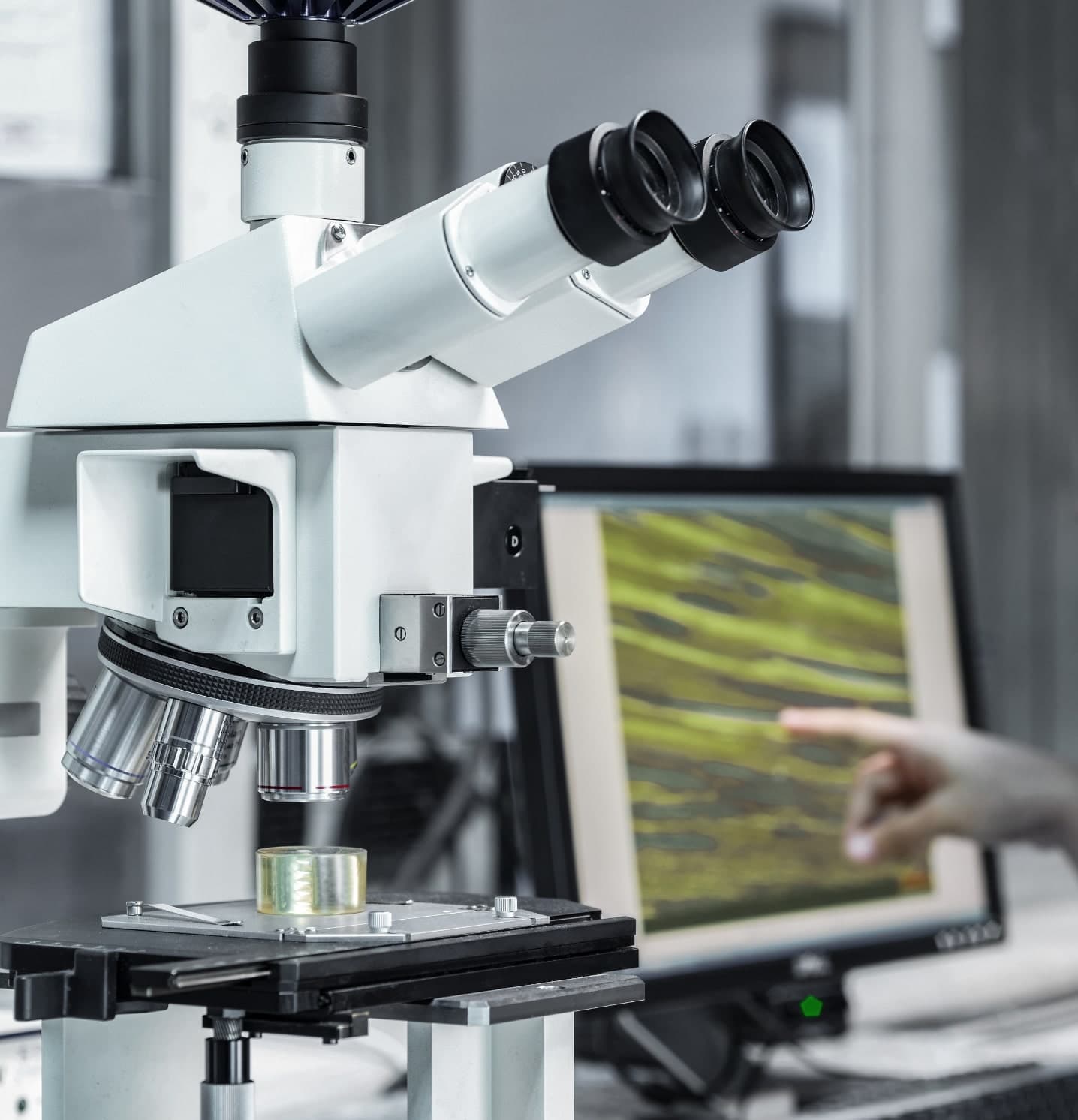
New research & development centre: AREAS
At our headquarters in Asola, we build a unique high-tech research and development centre of over 3,500 square meters. The state-of-the art testing infrastructure includes a climate wind tunnel, 3D body scanner and sports medicine department. This investment allows us to maintain and expand our technological advantage.
Find out more- 1950
- 1980
- 2003
- 2018